Many British towns and cities grew up around manufacturing. The north of England was once the production centre of the world during the industrial revolution. While manufacturing remained important to many cities until the 1970s, it has since been in prolonged decline.
The government wants to reinvigorate the sector, with larger conurbations such as Greater Manchester and the West Midlands being encouraged to develop local industry strategies.
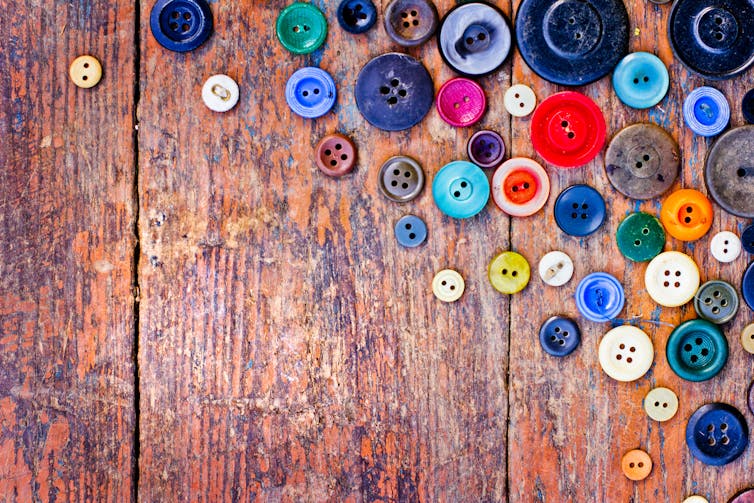
Talking to manufacturing firms in recent months, I have learnt three surprising things that local policymakers might take note of:
1. It’s hanging by a thread
Several textiles companies pointed out to me that there are no more button manufacturers in the UK. This came as a shock, considering how big an industry it used to be for Britain. A visitor to Birmingham, William Hutton, commented in 1780 on the “infinite diversity” of buttons manufactured there. But the last Birmingham button manufacturer, James Grove & Sons, closed down in 2012.
Responding to a June 2013 appeal featured in Country Life Magazine, a new company called Courtney & Co acquired the last remaining button-making machines from James Grove & Sons, drew on their heritage to learn the button-making trade and then relaunched production in the county of Gloucestershire. Some buttons can also be sourced from companies making other things, such as Ludlow Moulding, an injecting moulding company in Essex.
It seems strange that button making in the UK should be hanging by a thread, given that these small objects are so central to the clothing and accessories that we wear every day. But it is just one element of a steady hollowing out of the UK’s manufacturing supply chain since the 1970s, which could cause the country problems as it aims to rebuild its manufacturing economy post-Brexit.
This in part reflects the loss of machinery and technology, which was moved abroad, with supply chains following these machines to new centres of production in other countries. When it comes to buttons, the majority of the world’s supply now comes from towns such as Qiaotou in China, which is known as “button town” – just one of China’s many “one-product” towns – and produces around 60% of the world’s buttons.
2. Keeping things simple
Economies often progress by diversifying and becoming more complex. But this complexity can have downsides when it comes to environmental sustainability. Richard Horrocks, a professor of technical textiles at the University of Bolton, explained to me how many advanced and “blended” textiles are now proving hard to recycle as it is costly to break them back down into their component parts and give each part a new life. Acrylic is a particular no-no, given that we haven’t found a way to recycle this fabric.
Using products that are 100% from one source is more sustainable. In the past, fibres in 100% wool jumpers used to find new life in chair upholstery and then in carpets, before coming to the end of their life cycle.
Technical textiles are an excellent example of the type of advanced manufacturing that British cities are seeking to invest in. Developing complex processes and production chains based on simple raw materials might be one way forward.
One example of a highly effective but simple product is Ventile, first produced in Manchester at the request of Winston Churchill during the war to produce waterproof suits for bomber pilots. It is made from 100% cotton but its fine weaving process means that it is highly waterproof. Another example is Spacer Fabrics, which use one component (polyester) to create replacements for polyurethane foams, by knitting and layering fibres horizontally and vertically to create a springy material.
New processes for breaking down and reusing complex and blended materials (such as bug-based mechanisms for breaking down polyester) are also ripe for public and private investment and experimentation. Cities like Manchester, with its long history of both textiles and chemical production, could lead the way.
3. Sharing technology is vital
I heard a fascinating story recently from Numan Azmi, founder of the Manchester Knitters’ Association, about a revival of the knitwear industry that took place there following the decline of many of the mills and factories in the 1960s and 70s. This revival has largely been associated with productive networks of Asian family firms. But the sharing of technology has been instrumental to this story.
A local machine supplier started lending out knitting machines to local manufacturing firms, at no cost, until the firm made a profit. This spawned a whole series of knitwear firms that are still in production today, in addition to highly profitable e-commerce firms like Boohoo and Misguided.
Elsewhere, I have heard how important shared technology is to small firms for innovating and expanding in London. In the creative hub of Hackney, East London, many small firms spoke highly of the local Machines Room, which allows people to access a raft of different machines to experiment with new ideas and new production lines.
The Machines Room has been struggling in recent months due to high rental costs – part of a critical loss of affordable space for manufacturing in this high-cost city. These ventures are worth investment. They support innovation and collaboration among local firms with limited resources, while also offering learning and networking opportunities to the next generation of makers and manufacturers coming through our schools and colleges.
Francesca Froy, PhD Candidate, UCL
This article is republished from The Conversation under a Creative Commons license. Read the original article.