In underwater robotics, efficient buoyancy control is crucial for successfully operating autonomous underwater vehicles (AUVs). A team of engineering students from Rice University has developed an innovative solution to this challenge by harnessing the power of fuel cell technology.
Their project eventually led to the team creating a remotely operated underwater robot, demonstrating the potential for fuel cell-based buoyancy control devices (BCDs) to significantly reduce energy consumption and noise compared to traditional thruster-driven AUVs.
Traditional Buoyancy Control Methods and Limitations Conventional AUVs rely on thrusters, large pumps, and propellers to adjust and maintain depth. While effective, these methods have several drawbacks:
- High energy consumption
- Heavyweight components
- Increased operational costs
- Significant noise generation
These limitations have prompted engineers to seek more energy-efficient alternatives that can enhance the performance and endurance of underwater robots.
Fuel Cell-Based Buoyancy Control Device (BCD)
The Rice University engineering students’ project drew inspiration from an academic paper co-authored by their sponsor, Professor Fathi Ghorbel. The research explored reversible hydrogen fuel cells for buoyancy control, mimicking the function of fish swim bladders.
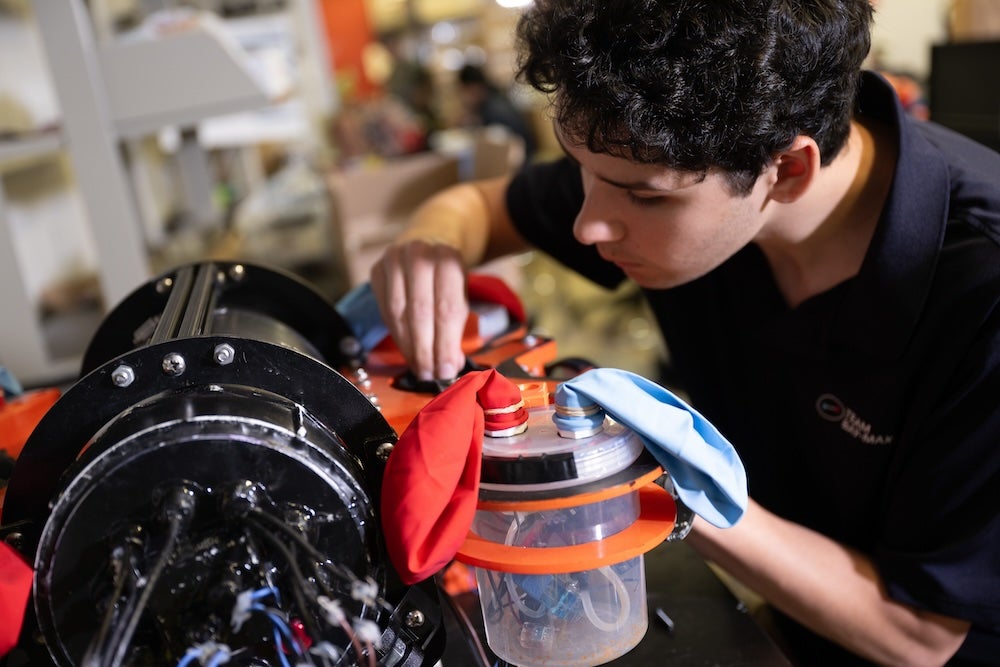
The BCD uses electricity to split water into hydrogen and oxygen gases, which are then stored in balloons. By controlling the amount of gas produced, the robot can adjust its buoyancy and depth with minimal energy expenditure. When the robot needs to descend, the process is reversed, with the fuel cell recombining the gases back into water, releasing energy.
The student team, including Andrew Bare, Spencer Darwall, Noah Elzner, Rafe Neathery, Ethan Peck, and Dan Zislis, collaborated to design and construct the prototype robot at the Oshman Engineering Design Kitchen. The project, spanning a year-long senior design capstone class, required the team to apply their diverse skill sets and knowledge in vehicle engineering and robotics.
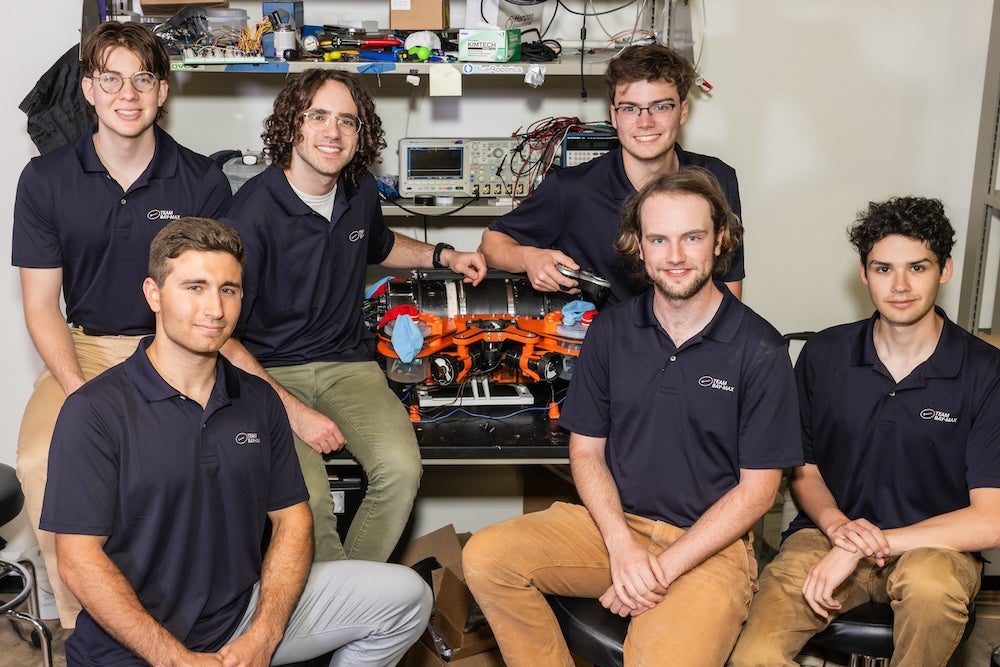
The robot, aptly named “BayMax,” incorporates several sensors that collect vital information about the system’s performance and the robot’s position and orientation underwater. This data is displayed on a user-friendly dashboard, providing real-time monitoring of the robot’s depth, orientation, and BCD activation state.
The fuel cell-based buoyancy control technology developed by the BayMax team has a wide range of potential applications extending beyond underwater robotics:
- Environmental monitoring
- Oceanographic research
- Military and industrial tasks
- Material Intelligence
- Assistive wearable devices
- Adaptive and reprogrammable robotic garments and fabrics
The project is part of a collaborative research effort involving Professor Ghorbel’s lab at Rice University, Professor Laura Schaefer’s lab at Rice, and Professor Zheng Chen’s lab at the University of Houston. This collaboration aims to develop tetherless continuum soft engines that utilize reversible proton exchange membrane fuel cells and water electrolyzers to drive volume-mass transformation.
The BayMax team faced various challenges throughout the project, particularly in managing system interdependencies. The team emphasized the importance of defining a clear project scope and making strategic decisions to focus on the buoyancy control device’s core technology.
The students also highlighted the valuable learning experiences gained from the project, including delving into control theory, software development, and the practical application of engineering principles. The project’s success, recognized with a second-place finish in the Willy Revolution Award for Outstanding Innovation at the annual Huff OEDK Engineering Design Showcase, is a testament to the team’s dedication and problem-solving skills.
If it can be scaled up commercially, this technology has the potential to significantly enhance the capabilities and performance of AUVs, enabling more extended missions, reduced operational costs, and expanded applications in various domains.
TLDR:
- Rice University engineering students developed an underwater robot with fuel cell-based buoyancy control
- The buoyancy control device (BCD) uses reversible hydrogen fuel cells to adjust depth efficiently
- The technology mimics fish swim bladders and offers a quieter, more energy-efficient alternative to thruster-driven AUVs
- Potential applications include environmental monitoring, oceanographic research, and military and industrial tasks
- The project is part of a collaborative research effort involving multiple universities
- The team overcame challenges in system integration and project scope definition, gaining valuable learning experiences