Slithering through rubble and debris, a robotic snake winds deep inside a collapsed building. Guided by algorithms and remote sensors, it deftly navigates tight spaces and shifting wreckage. Behind it, a rescue worker monitors the feed from its camera eyes, searching for trapped victims.
Scenarios like this demonstrate the immense promise of snake-inspired robots. With slender and nimble bodies, they can access confined areas that are impossible for humans or traditional robots. However, stability, precision, and accuracy issues have limited their real-world deployment.
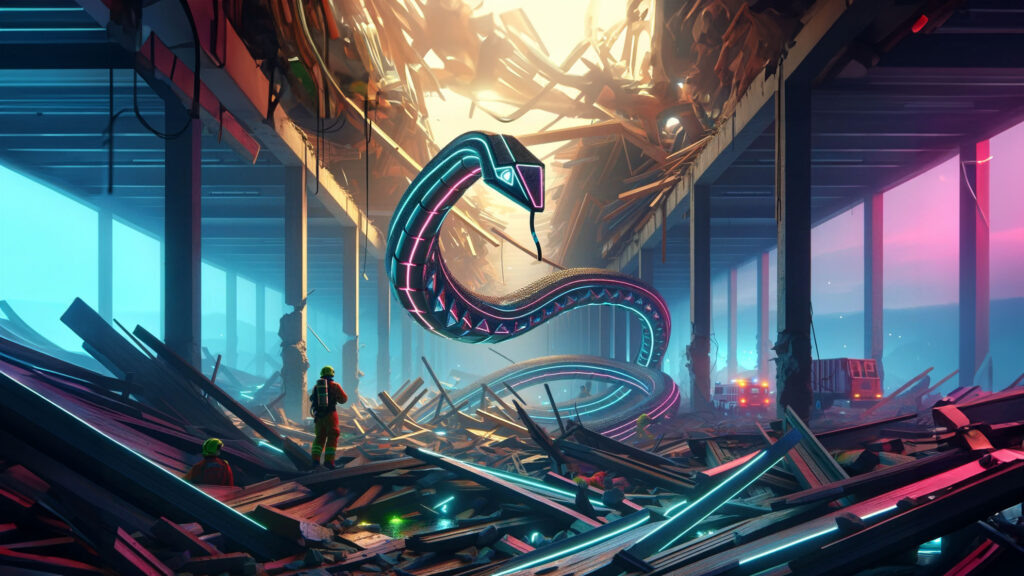
Researchers from Lancaster University, Beijing Institute of Technology, and North China University of Technology recently developed an innovative strategy to improve snake robots’ positioning accuracy substantially.
Their “macro-micro” approach combines adjustable mechanical stiffness with comprehensive mathematical friction and cable forces modelling. Physical experiments demonstrated an average of 183.4% accuracy gains under payload. This breakthrough brings snake robots closer to assisting in disaster recovery efforts, infrastructure inspection, and other challenging tasks.
Why Snake Robots? Navigating Complex Environments
Snake robots provide unique capabilities beyond conventional wheeled or legged robots. With narrow diameters and many articulated joints, they can traverse tight, twisting spaces. This lets them access areas impossible for humans, whether inside rubble, pipelines, aircraft engines, or human bodies during surgery.
Small snake robots have already demonstrated some real-world use. For example, the Olympics used one to inspect infrastructure before the 2022 Beijing Games. However, most research focuses on theoretical work or single-section prototypes less than 0.5 meters long. Achieving operational accuracy with more giant multi-section snake robots remains an open challenge.
Precision and stability issues currently limit the broader adoption of snake robots. As length increases, flexibility reduces stiffness, causing positioning errors. This notably limits the accurate manipulation of tools or sensing devices at the tip. Solving these issues while retaining snake robots’ ability to “shape-shift” based on environment constraints became the research team’s focus.
A Bioinspired “Macro-Micro” Design Strategy
To improve snake robots’ confined space accuracy, the team developed a “macro-micro” approach inspired by animal manipulation abilities. The modular design divides functionality between initial navigation (“macro”) and final precision tasks (“micro”).
The snake robot comprises three short but highly flexible tip sections for precision adjustment and seven longer mid-body sections for coarse positioning. This mimics an elephant’s trunk – able to lift cargo with the strength of base segments while manipulating small objects with distal tips.
Both tip and mid-body sections have two articulated joints. However, their actuation strategies differ. Tip joints move independently, avoiding interference between cells to enhance fine control. Mid-body joints use a coupled approach that runs cables from the tips back down the length of the robot. This improves overall stability and reinforces accuracy gains from the precision tip.
An additional novelty comes from the quick-release end connector that facilitates rapidly swapping sensor payloads and tools. This expandability allows one snake robot design to serve multiple purposes.
Regulating Stiffness with Adjustable Cable Tensions
While the modular design defines the snake robot’s physical architecture, adjustable cable tensions enable tuning its stiffness. Each joint has three active cables akin to tendons that pull to actuate movement. Regulating pressure varies resistance to loads, much like contracted muscles stiffen limbs.
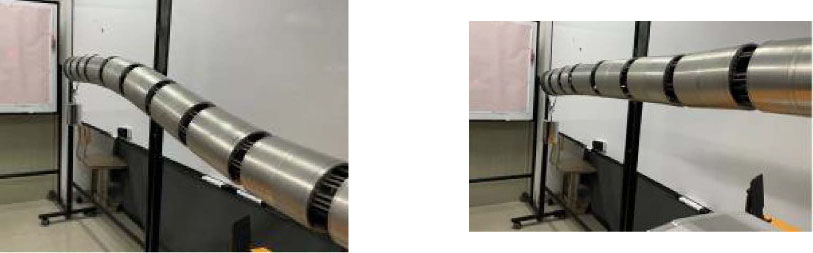
Higher tensions improve precision and introduce tracking errors from cable forces and friction. Therefore, the team developed a comprehensive kinetic and static model balancing these factors. It captures intricate mechanical interactions using parallel manipulators and structural beam deflection principles.
The model uses inverse kinematics to map cable lengths to joint angles. It incorporates data on mass distribution, motor torques, expected loads, friction coefficients, and factors derived from the macro-micro segmented design. These inputs simulate tension distribution impacts on each section’s deviation.
Several innovations bolster model accuracy:
- When calculating tension propagation down the robot, consider cable stiffness variation and internal friction. Both reduce forces, affecting equilibrium.
- Modelling parasitic loads in mid-body segments from tip section cables running through their joints. Increased tension magnifies these disturbances.
- Formulating stiffness matrices based on cable vectors and central structural supports. Tension changes dominate, determining system pliability.
The team could mathematically optimise tensions before testing to evaluate real-world prototype performance under different cable preloads. This provided data to improve modelling fidelity iteratively.
Prototyping and Validation Testing Confirms Precision Improvements
With analytical work established, the next phase focused on constructing a working experiment prototype. The final design used stainless steel driving cables and a modular gripper payload with integrated sensors. An active linear stage handled coarse repositioning.
Each of the 20 joint actuators had a dedicated control circuit, allowing software adjustment of target angles and cable tensions. This enabled easy reconfiguration between tests for a given shape. It also facilitated tension modulation studies with the manipulator straight or bent.
Results validated the model’s effectiveness, showing substantial improvements in accuracy and deviation reduction by increasing cable loads. On average, doubling tension improved stiffness between 49-54% in the tip section for straight and bent mid-body postures.
Interestingly, experiments revealed that coupling between segments creates an amplification effect. This causes base segment tension modulation to cascade down the arm, benefiting tips. The tests also provided data to refine friction and torque assumptions. By the final incarnation, the model achieved over 96% prediction accuracy.
Researchers also compared performance to common biological stiffness control mechanisms. These approaches use heat or pneumatics to lock segments together. However, they require running actuators constantly or complex air supply logistics. The cable tensioning strategy achieves a similar dynamic range without these downsides, highlighting its advantages.
Future Applications
The novel cable-tensioning “macro-micro” design strategy demonstrates a clear pathway to unlocking snake robots’ full potential. Extensive modelling aligned with experimental validation tackles previous roadblocks. This research provides a recipe for accurately incorporating real-world factors into performance estimates.
By demonstrating significant and consistent improvements under loaded conditions, the prototype snakes show readiness for rigorous real-world testing. The subsequent efforts will focus on constructing larger systems and evaluating capabilities in relevant environments. Success could see snake robots assisting humans in disaster zones, conducting infrastructure inspections, or enabling less invasive surgical techniques.
This breakthrough helps move biologically inspired robotics from theory into practice. As early computers progressed from laboratory curiosities to indispensable tools, snake robots may soon permeate engineering challenges requiring dexterous navigation of confined spaces. If so, they will save lives and drive progress through resilient infrastructure – all while displaying nature’s timeless wisdom. The future slithers forward on robotic scales.
TLDR:
- Snake robots are helpful for complex environments, but accuracy issues currently limit deployment
- New “macro-micro” design strategy and adjustable stiffness proposed
- Mathematical modelling incorporates friction and cable forces
- Prototype testing shows a 183% accuracy improvement, confirming the model
- Enables future snake robots for search/rescue, infrastructure inspection, etc.