Small satellites, like CubeSats, are gaining momentum, given their affordability and customizability. However, these pint-sized satellites have a big problem – they need more capable propulsion systems to move them once in space. Without manoeuvrability, nanosats that have completed their missions turn into dangerous space junk with no way to deorbit. As more small satellites reach orbit, experts warn we may soon face a tipping point for collision-induced space debris.
A Spanish company has engineered a solution that promises precision control and sustainability even for the smallest satellites. Using an electric propulsion technology called “electrospray,” their ATHENA micro thrusters can steer tiny satellites while preventing them from cluttering up space at the end of their lifespan.
What is Electrospray Propulsion?
Electrospray propulsion relies on extracting and accelerating charged particles to generate thrust. An electrostatic field propels ionized particles outwards from a conductive liquid fuel flowing through an emitter.
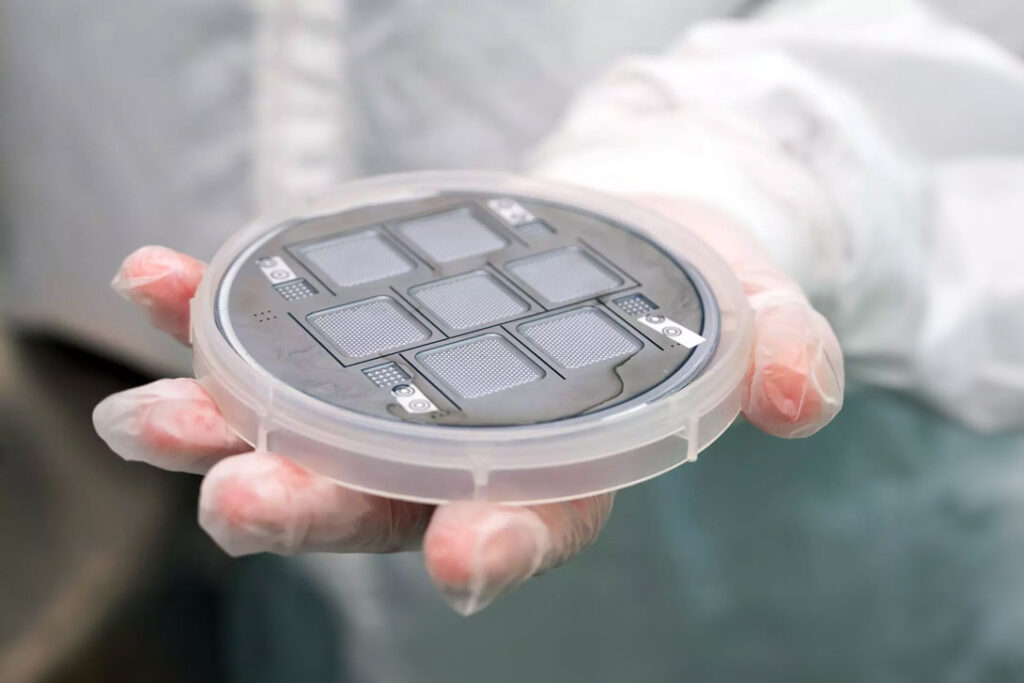
This method promised “high propulsive efficiency” and precise controllability with minimal power draw. In theory, these types of thrusters have compact, straightforward designs since no pressurized propellant tanks are involved. Their small size, low mass, and modular architectures make them ideal for the growing nanosat segment.
Depending on the fuel and operating conditions, the ionized spray comprises either charged liquid droplets or pure ions. Using ionic salt propellants provides flexibility – ATHENA thrusters can emit positive and negative ions to neutralize the satellite’s charge. Clustering multiple emitters together scales up thrust, enabling custom configurations.
Engineering a Scalable Solution
ATHENA stands for Adaptable Thruster based on Electrospray powered by Nanotechnology. The significant advantage of the new tech is that these types of microfabricated silicon thrusters are inherently customizable thanks to IENAI Space’s proprietary manufacturing techniques.
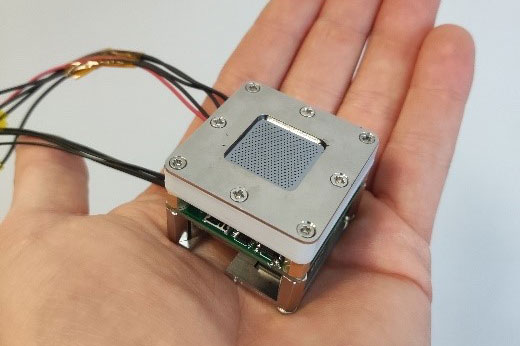
Etching emitter arrays onto silicon wafers through micro- and nanofabrication allows consistency with the original designs. This accuracy lets engineers fine-tune operating parameters for optimal efficiency. While each thruster possesses over 500 emitting holes, they only need a face area of 10 cm x 10 cm – the size of a single CubeSat unit.
The company worked in parallel on a software solution to handle the vast configuration options. Considering satellite and mission parameters, it recommends customized ATHENA setups grouping individual units. Six thrusters fit on one CubeSat face and can scale up to steer 50 kg spacecraft using thruster clusters.
Besides ensuring reliable and robust production, ESA funding facilitated a complete engineering test regime. This qualification process verified that ATHENA survives the harsh space environment for extended durations. The current breadboard model has already demonstrated over 400 hours of continuous firing.
Applications and Impact
The adaptability and precision control that ATHENA enables have two profound implications – responsible debris mitigation and expanded satellite manoeuvrability:
- Deorbiting Defunct Satellites at End-of-Life
- Without propulsion, small satellites remain in crowded orbits even after malfunctioning. ATHENA provides the thrust needed to safely deorbit them by lowering altitudes. Preventing derelict nanosats eliminates a rising source of space junk.
- Enabling Maneuverability for New Missions
- The same precision and efficiency that aids deorbiting allows new steering capabilities. Small satellite operators can leverage ATHENA’s flexible thrust configurations to expand mission scopes like stationkeeping, orbital transfers, and attitude control.
These two applications promise sustainability and are particularly important for future satellite constellations that can provide new services without cluttering space for future generations. They also make satellite infrastructure collision-resistant by dodging debris. Experts consider this active debris mitigation essential for continued access and operations in vital orbital zones near Earth.
Next Steps
Having passed the preliminary design review after its 2023 kickoff, the ATHENA electrospray propulsion system remains on track for qualification by the end of 2024. Upcoming work focuses on validating reliability and performance to spaceflight standards.
As one of just a handful of European electric propulsion products catering to small satellites, early market response remains promising. The flight-proven concept already has the interest of several satellite manufacturers.
If successful, the microscale but high thrust levels feasible demonstrate electrospray propulsion’s potential suitability for an even broader range of spacecraft sizes. ATHENA promises sustainable and precise manoeuvrability down to tiny CubeSat scales that are affordable for private operators by using scalable electrospray technology paired with modular microfabricated thrusters. If successful, such microscale but high-thrust propulsion could democratize capabilities previously restricted to only large, expensive satellites.
TLDR
- Small satellites like CubeSats are gaining popularity but face limitations in manoeuvrability and disposal
- Without propulsion, defunct nanosats turn into dangerous space debris, cluttering up critical orbits
- Electrospray propulsion technology uses ionized particle spray extraction to generate precise thrust
- ATHENA micro thrusters developed in Spain custom-fit electrospray propulsion to tiny CubeSat scales
- Clustering multiple emitters provides flexible scalability for various satellite sizes
- The software helps recommend optimized ATHENA configurations for different mission parameters
- Microfabrication enables accuracy and efficiency, while proprietary methods ensure reliability
- The tested breadboard model exceeds 400 hours of continuous firing and is on track for qualification by late 2024
- Enables affordable precision control for expanded satellite capabilities and collision avoidance
- Promises sustainable small satellite infrastructure through end-of-life deorbiting capability