HS2’s first Tunnel boring machine (TBM) named “Florence” has broken through the chalk geology of the Chilterns Hills in Buckinghamshire, UK, completing a 10-mile drive and excavating the longest Tunnel on the high-speed rail project.
The breakthrough took place on February 27th, 2024, and marks a significant milestone for the HS2 line, which will dramatically reduce journey times between London and Birmingham when completed in 2029.
The 5.6m diameter Florence is one of two Herrenknecht TBMs tunnelling parallel passages under the Chilterns to create the twin-bore Chiltern Tunnel. Crews steering the 2,000-tonne mega-machine round-the-clock excavated through chalk and flints at an average pace of 16 meters per day since its launch in May 2021 from the South Portal.
The tunnels aim to provide a vital link cutting through a protected landscape that has slowed the rail connection between the UK’s two largest cities. Florence lined the tunnels with 56,000 curved concrete segments as it advanced, while teams at the surface processed over 3 million m3 of chalk spoil from the tunnelling.
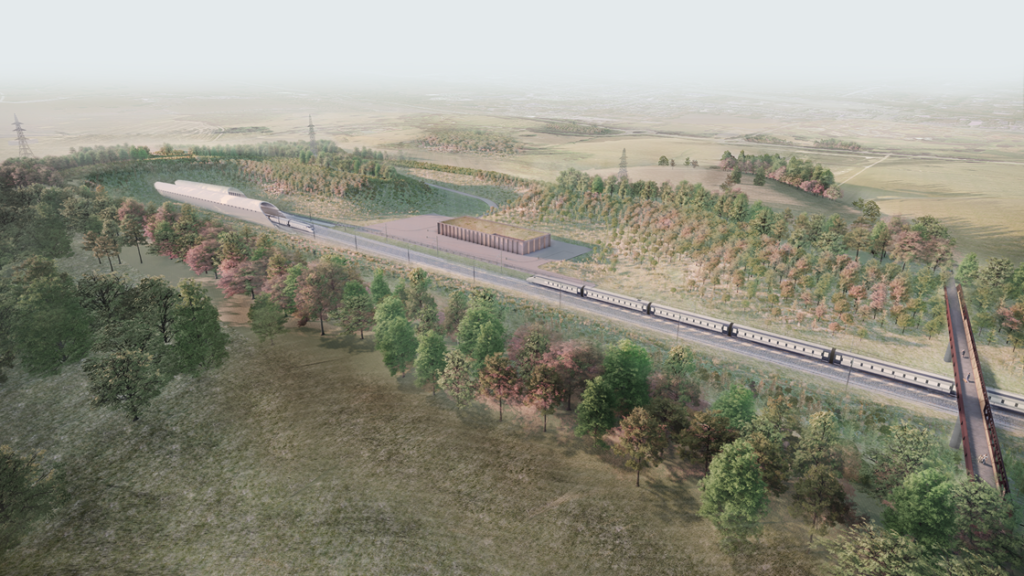
Rail Minister Huw Merriman said, “HS2 will dramatically improve journeys between our two largest cities and free up space on the existing mainline for more local trains.” The project is expected to spark a £10 billion economic boost around its stations over the next decade.
The twin tunnels under the Chilterns reach depths 80 meters below ground at the deepest point, passing beneath local transport routes and the River Misbourne twice. Water quality and environmental monitoring during construction have shown no significant impacts thus far.
After 2 years and 9 months of progressing through the varied geology since launch, Florence’s breakthrough at the North Portal near South Heath marks a successful tunnelling accomplishment. Florence’s sister machine, Cecilia, is soon anticipated to go through as well, showing the momentum the ambitious HS2 project is now gaining.
HS2 Boring Machine Names: How did Florence get her name?
The naming tradition for HS2’s massive Tunnel boring machines recognizes groundbreaking women across science, medicine, education, engineering, and literature. The chosen names highlight female trailblazers localized to the areas the TBMs are excavating under, showcasing diverse representation spearheaded by local schools and communities.
The first two machines – Florence and Cecilia – hold names suggested by students based on early female medical and scientific discovery pioneers. Florence Nightingale’s innovations in modern nursing and statistical diagrams blazed a trail for evidence-based care and public health reforms. Cecilia Payne-Gaposchkin’s revolutionary work in astrophysics and stellar atmospheres made her the first person to receive a PhD from Radcliffe College. They shifted their understanding of the composition of stars.
Other machines along the route honour women like Dorothy – named for the first female professor at a UK university, Dorothy Hodgkin – and Caroline Herschel, an astronomer who discovered stars and comets, often working side by side with her brother William Herschel. Emily Sophia Taylor and Anne Byron were also recognized for expanding maternity health services and bringing early education to underserved groups in 19th-century England.
The depth of impact these forward-thinking women had across literature, education, justice, infrastructure, and space sciences is mirrored by the immense scale of engineering HS2’s TBMs are achieving underground. Their names etched into the tunnelling machines are a tribute to the ground they broke and the paths they laid in their times that continue to inspire today. HS2’s choice to uphold pioneering females through this tradition celebrates history and diversity while building towards more innovative and inclusive futures.
The Engineering Behind Tunnel Boring Machines
Tunnel boring machines (TBMs) have revolutionized the way tunnels are constructed since the introduction of the first such device in the 19th century. Originally designed as an alternative to more dangerous traditional mining techniques, these underground drilling machines have enabled transportation networks, infrastructure projects, and connections unimaginable without them.
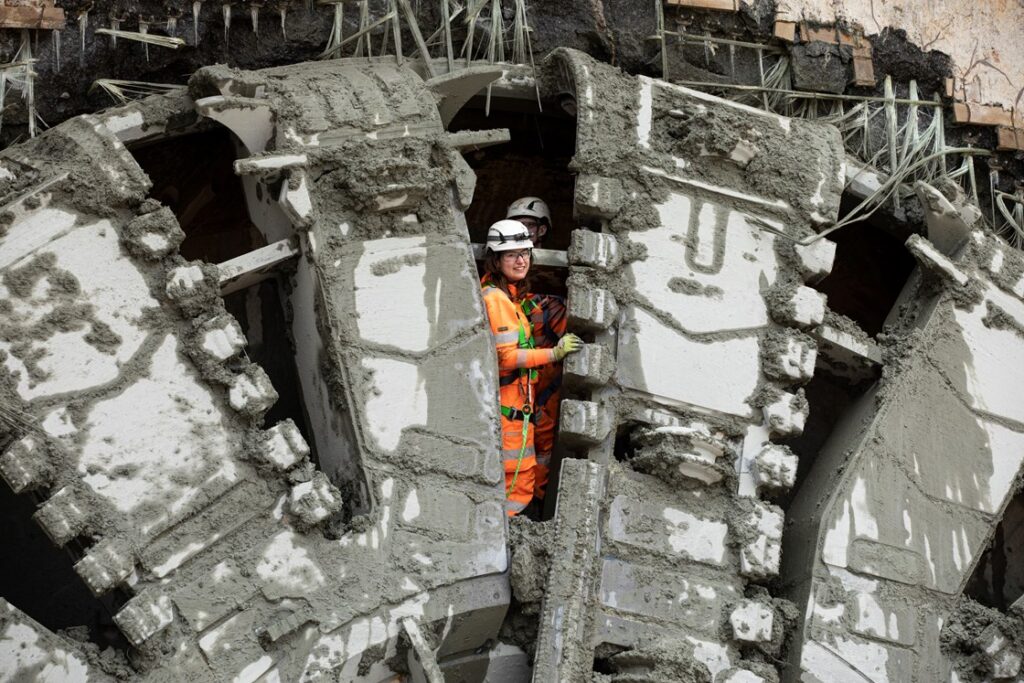
The first recognizable TBM was created by Sir Marc Isambard Brunel in 1825 to assist in digging a tunnel under the Thames River. It consisted of metal shielding that protected workers as shovels and pickaxes slowly carved through dirt and soft clay. This was a significant upgrade from the previous failed attempts using essential tools, though still manually powered and highly labour-intensive.
Modern TBMs still retain a cylindrical outer shield but are now entirely mechanized with advanced drilling heads and conveyor systems to remove debris. Giant rotating cutters grind through earth and rock while hydraulic propulsion jacks push the machine forward. The circular Tunnel is simultaneously lined with curved concrete or metal segments for support. A small crew oversees operation and logistics but no longer needs to perform manual excavation.
How Tunnel Boring Machines Work
The key functionality of any TBM revolves around its sizeable rotating cutter head. Made up of disc cutters and complex rock tools like tungsten carbide, the spinning action fractures the substrate while applying tremendous pressure. Conveyors then capture loose sediment, transporting it backwards via a screw auger or belt as the machine advances.
Integrated tunnel segment erectors follow to immediately install concrete voussoirs, pie-shaped walls that interlock to form rings. Gaps are filled with grout for stability. Once a call is set, the TBM pushes off it using hydraulic jacks to drive itself forward. This simultaneous boring and lining make tunnelling much more efficient.
Types of Tunnel Boring Machines
There are two main categories of TBMs – those designed for hard bedrock and those tailored for soft ground or soil.
Tunnelling machines lack any shielding, bracing themselves through gripper pads against the bare tunnel walls. Thrust cylinders transfer power directly to the cutter head. They are well suited for stable, consolidated rock needing little extra support during or after excavation.
Shields have a protective outer chassis to shore up looser surrounding material temporarily. They facilitate the installation of the final concrete or steel ring reinforcements for long-term strength. Additional subclasses include:
- Open shields without enclosed volume
- Closed front with removable gate
- Slurry shields using pressurized bentonite mud
- Earth pressure balance (EPB) TBMs
Double shields are a hybrid, configurable to operate in either mode. This flexibility is functional when geology changes frequently.
Modern TBMs are enormous, spanning over 100 meters in length and weighing thousands of tonnes. They function as underground factories – drilling, excavating, and fortifying tunnels while pushing forward. Diesel generators provide power across sections.
The rotating cutter head forms the working face, studded with rugged disc cutters and other rock cutting tools. Diameters range from one meter for micro TBMs up to 19 meters for mega projects.
Onboard crews operate in shifts to keep the machine running 24/7. There are three leading roles:
- Pilot – oversees all TBM functions
- Mechanic – maintains cutters, conveyors, hydraulics
- Technician – monitors tunnel wall integrity
Additional surface crews handle logistics like material transport and crane operation.
TBMs provide advantages unachievable otherwise when building tunnels. Boring machines reduce environmental impact, make excavation safer compared to traditional methods, and their capabilities will only improve. The continued evolution of cutter head technology and conveyor mechanisms paints an exciting future for connecting cities and countries through underground pathways.
Today’s breakthrough enables the subsequent phases of work at the North Portal, but much activity remains ongoing at other active tunnelling sites and viaduct construction zones along the route. The arrival of high-speed rail in UK regions is set to trigger opportunities for connectivity, regeneration and integrated growth strategies building on HS2’s capabilities in the years ahead.
TLDR:
- HS2’s first TBM “Florence” broke through after a 10-mile dig under the Chilterns
- The breakthrough marks a significant milestone for the UK’s high-speed rail project
- The twin-bore Chiltern Tunnel is the longest on the HS2 line at 16km
- HS2 will reduce travel times between London and Birmingham by up to half
- The tunnelling churned through chalk geology at an average of 16m daily
- Crews lined the Tunnel with 56,000 concrete segments during the 2-year, 9-month drive
- The project is expected to spark significant economic growth around stations